Facilities Overview
Arnold Magnetics Corporation modern 25,000 square foot facility, located in Camarillo, CA, is Corporate Headquarters for our complete operation. All off-the-shelf standard and custom power conversion products are manufactured and tested to detailed requirements and each unit receives a comprehensive burn-in prior to shipment. The incorporation of standard high density power products, allows us to offer timely, cost effective, configurable power solutions, tailored to the unique power application. The use of this “Rugged COTS” technology, coupled with our attention to detail, ensures high reliability and peak performance for our Military, Industrial, and Aerospace industry customers. Our highly experienced Research and Design Team, offers competitive, leading edge technology solutions, using our comprehensive database of standard and customized designs. Advanced power electronics design techniques are utilized to meet the most demanding requirements!
Engineering and Product Development
Develops and qualifies rugged standard and custom AC-DC, DC-DC, DC-AC power converters and inverters for COTS manufacturing and program management for customer applications including:
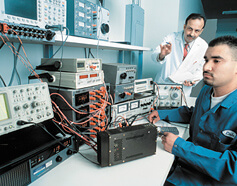
- Power system design and assembly
- Breadboard – brass board - prototype development
- Telemetry control circuitry
- Mechanical design of enclosures, interconnects, power and thermal management
- Input and output EMI filtering to MIL-STD 461C-G and DO-160 requirements
- Spike and transient suppression to MIL-STD 704, 1275 and DEF STAN 61-5 requirement
- High power conversion efficiency, low profile, light weight and high power density
- Wide -55°C to +85°C baseplate operating temperatures.
Manufacturing
Develops and qualifies rugged standard and custom AC-DC, DC-DC, DC-AC power converters and inverters for COTS manufacturing and program management for customer application including:
- Magnetics Department
Power transformer and EMI filter magnetics are produced using processes and controls that have been established and refined over the last 60 years. - Production / Sub-assembly
Production assembly utilizing - through-hole assembly - Surface mount assembly, all to IPC-610 and J-STD-001. Class III requirements available. - Test Department
Sub-assemblies and completed assemblies manufactured at AMC are subjected to minimum test criteria using 100% sampling. All power supplies manufactured by AMC are also subjected to a minimum burn-in and power cycling criteria. - Fabrication
AMC maintains a fully functional machine shop in order to accommodate: Prototype, Pre-production metal work, C &C. (Full rate production is provided via qualified external suppliers)
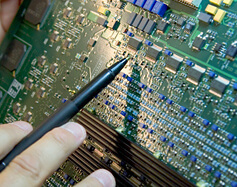
Test Capabilities
EMI Testing
- Mil-Std-461C-G Conducted Emissions testing on-site
- LISN’s for Single and Three Phase
- Spectrum Analyzers
- Computerized test data and limit curves
Acceptance/Design Verification Testing
- Spectrum Analyzers
- Digital Oscilloscopes
- Function Generators
- Hi-Pot Testers
- Programmable AC and DC Power Sources
- Frequency Generators
- Unique and Standard Load Test Equipment
- Multi-frequency high power generators
- Programmable Loads
- Intelligent Platform Management Interface (IPMI)
- Transient Voltage
Environmental Testing
- Mil-Std-810 – Shock, Vibration, Salt Fog, Fungus, Humidity, Temperature,
Explosive Atmoshere, Fungus, Altitude, Sand, Dust, Acoustic Noise - Mil-461C-G conducted emissions testing on-site
- Mil-Std-167 Shipboard Vibration
- Mil-S-901C Shock
Quality Assurance
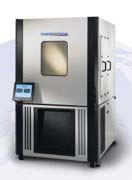
Environmental Stress Screening
- Internal ESS Lab to support and confirm additional product reliability
- Vibration Equipment for: Shock, Random, Sinusoidal
- Temperature Chambers for: Temperature Cycling, Fast Temperature ramp, High/Low Temperature Operation
Quality Control
- Inline Statistical Process Control, Statistical Product Monitoring,
- Average Outgoing Quality Data
- Receiving Inspection to ISO 9001
Procedures and 100% In-process and Final inspection criteria.